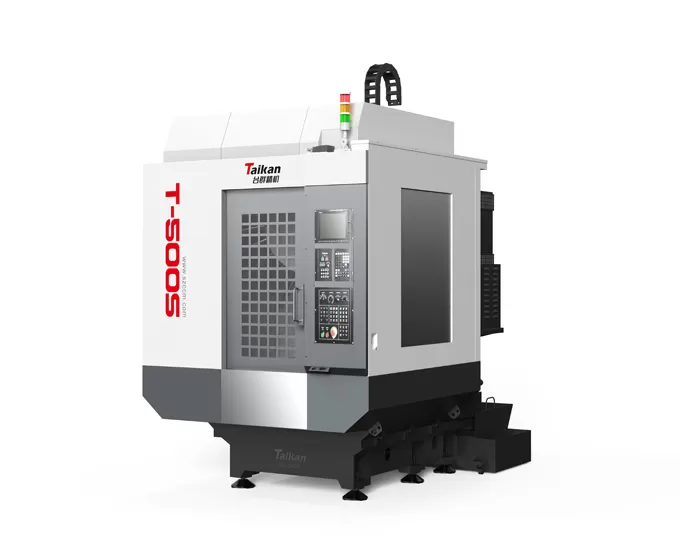
Drilling & Tapping Machining Center
Unmatched value for money Exceptional stability High reliability
Base Structure
The base structure is designed with digital analysis and precision engineering, featuring an oversized span with six-point support, effectively enhancing the machine's rigidity and vibration resistance, ensuring high stability and accuracy during the machining process.
X, Y, Z Axes
All three axes are equipped with precision ball screws, and the guide rails use high-precision linear guides, ensuring smooth operation and precise positioning for outstanding machining accuracy and reliability.
Direct Drive Spindle
The spindle features a direct-drive transmission system, reducing errors in high-speed tapping and ensuring excellent performance with high output power in high-speed machining.
The high-speed spindle responds quickly and is equipped with ceramic ball bearings, significantly extending spindle life.
The precision-grade spindle is standard with a maximum speed of up to 20,000 rpm, meeting the demands of high-precision and high-speed machining.
High-Speed Servo Tool Changer
The optimized PLC tool changer system provides a fast and stable tool change process, significantly reducing tool change time and non-machining time, thus improving overall machining efficiency.
The Z-axis is designed with optimization to enhance rigidity and significantly improve acceleration, reducing idle travel time and further increasing machining efficiency and machine responsiveness.
The machine tool is suitable for the multi-variety, small-batch processing of complex parts such as medium and small-sized box-shaped components, plates, disks, valves, housings, and molds. It is widely used in industries such as precision parts, 5G products, hardware, automotive parts, and medical devices.
Workpiece Example 1
Workpiece Example 2
Workpiece Example 3
Workpiece Example 4
Workpiece Example 1
Workpiece Example 2
Workpiece Example 3
Workpiece Example 4
Workpiece Example 1
Workpiece Example 2
Workpiece Example 3
Workpiece Example 4
Item | Unit | T-500S | Remarks | ||
Travel | Table travel (X axis) | mm | 500 | ||
Saddle travel (Y axis) | mm | 400 | |||
Headstock travel (Z axis) | mm | 320 | |||
Distance from spindle nose to table surface | mm | 180-500 | |||
Distance from spindle center to column guide surface | mm | 445 | |||
Table | Table size | mm | 620*400 | ||
Max. load | kg | 250 | |||
T-slot (number of slots - slot width * spacing) | mm | 3-14*120 | |||
Spindle | Motor power (rated/short time) | kW | 3.7/5.5 | ||
Motor torque (rated/short time) | N.m | 14.1/21 | |||
Spindle motor speed | rpm | 20-24000 | |||
Spindle taper | / | BT30 | |||
Speed | Cutting feed speed range | mm/min | 1-15000 | ||
X/Y/Z axis rapid traverse speed | m/min | 48/48/48 | |||
Accuracy | Positioning accuracy (X/Y/Z) | mm | 0.006 | GB/T 18400.4(Full travel) | |
Repeatability (X/Y/Z) | mm | 0.004 | |||
Tool magazine | Tool storage capacity | pcs | 21 | ||
Max. tool weight | kg | 3 | |||
Max. tool length | mm | 300 | |||
Max. tool diameter (full /adjacent empty) | mm | Ф60/Ф80 | |||
Other | CNC system | Mitsubishi M80VA | |||
Air source | Flow | L/min | ≥200(ANR) | ||
Air pressure | MPa | 0.6-0.8 | |||
Equipment capacity | kVA | 15 | |||
Max. coolant tank capacity | L | 145 | |||
Machine size | mm | 1660*2480*2330 | Corresponding to X*Y*Z axis | ||
Weight (approx.) | kg | 2800 |
The information on this page is for reference only. Specifications and details may change due to product upgrades or improvements. For more information, please contact us.
Mitsubishi
FANUC
Siemens
Taikan
Apr 11 2025
Apr 01 2025