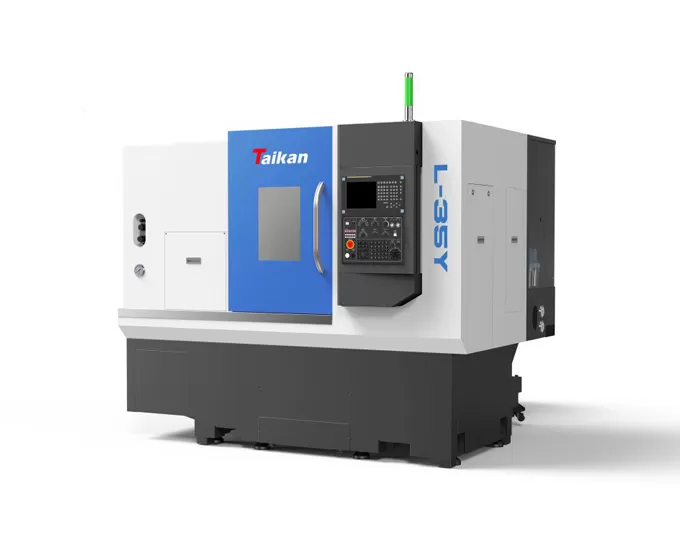
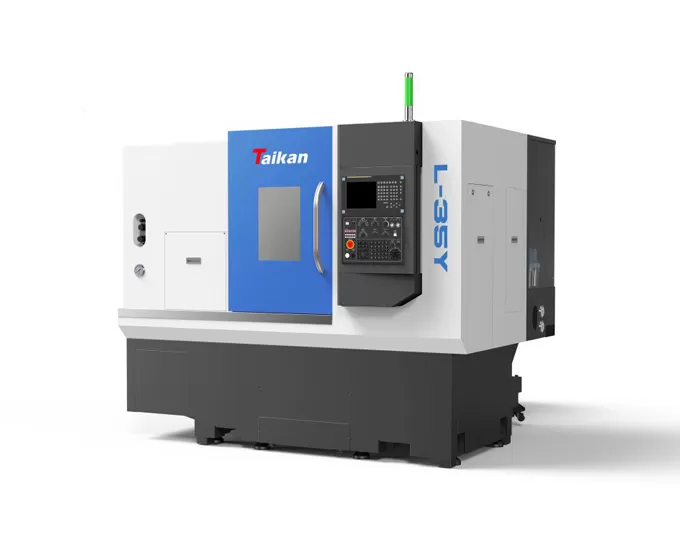
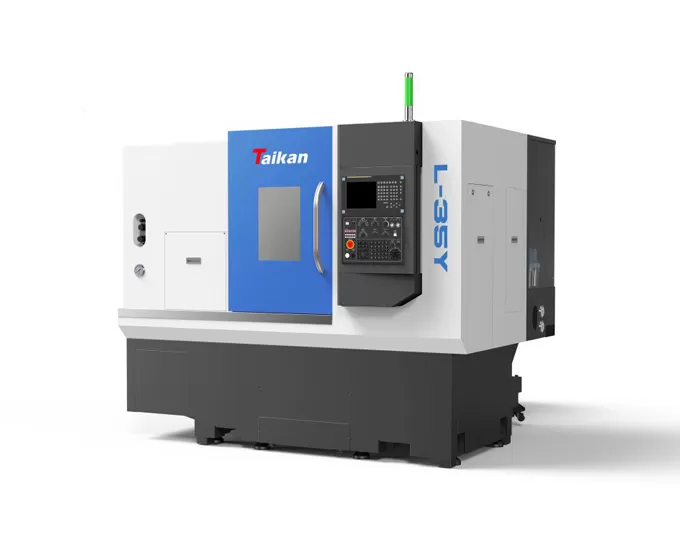
High rigidity, high stability, high load-bearing capacity
Overall
The machine has an integrated layout of machinery, electricity and hydraulics, and an overall inclined bed, which has the advantages of compact structure, high rigidity, smooth chip removal, and easy operation.
Guide Rail
The guide rails are of the rolling type, and the drive components use high-speed, quiet ball screws, offering fast speeds, low heat generation, and high positioning accuracy.
Spindle
The main transmission system of this machine adopts high-performance, high-torque spindle transmission, with a spindle speed range of 0-4000r/min.
Tool
This machine adopts BMT55 powered turret (including Y-axis), which has fast tool changing speed and high reliability; it is equipped with axial and radial powered tool holders to meet milling needs.
This lathe meets the needs of complex parts processing and is widely used in valves, ships, engineering machinery and other fields, especially favored by automotive parts manufacturers.
Workpiece Example 1
Workpiece Example 2
Workpiece Example 3
Workpiece Example 4
Items | Unit | L-35Y | Remarks | |
Processing range | Max. rotation diameter | mm | φ520 | |
Max. processing diameter (axis/plate) | mm | φ300/φ350 | ||
Max. processing length | mm | 330 | ||
Max. bar diameter | mm | Φ52 | ||
Travel | X –axis travel | mm | 200 | |
X –axis motor power/stall torque | kW/Nm | 1.8/11 | ||
Y –axis travel | mm | 100(±50) | ||
Y –axis motor power/stall torque | kW/Nm | 1.8/11 | ||
Z –axis travel | mm | 400 | ||
Z –axis motor power/stall torque | kW/Nm | 1.8/11 | ||
Spindle | Output power(S1/S6) | kW | 11/15 | |
Spindle end form | A2-6 | |||
Spindle rotary speed | r/min | 0-4000 | ||
Hole diameter | mm | Φ63 | ||
Chuck | Hydraulic 3-jaw chuck | inch | 8 | Hollow |
Tailstock | Tailstock sleeve diameter/travel | mm | Φ70/100 | Optional |
Tailstock sleeve taper hole | Morse | Morse 4# | Live center | |
Speed | X-axis rapid traverse speed | m/min | 30 | |
Y-axis rapid traverse speed | m/min | 10 | ||
Z-axis rapid traverse speed | m/min | 30 | ||
Cutting Feed Rate | mm/min | 1~8000 | ||
Tool holder | Tool capacity | T | 12 | |
Milling head motor power/stall torque | kW | 2.7/12-46 | αi S 12/4000-B | |
Milling tool max. speed | r/min | 4000 | ||
Milling tool handle specification | mm | BMT55 | ||
Turning tool holder specification | mm | 25×25 | ||
Max. boring tool diameter | mm | Φ32 | ||
Accuracy | X axis positioning accuracy | mm | 0.006 | |
Y axis positioning accuracy | mm | 0.02 | ||
Z axis positioning accuracy | mm | 0.006 | ||
C axis positioning accuracy | arc sec | 51 | ||
X axis repeatabilitys | mm | 0.004 | ||
Y axis repeatability | mm | 0.005 | ||
Z axis repeatability | mm | 0.004 | ||
C axis repeatability | arc sec | 20” | ||
Others | Power Supply Capacity | kVA | 30 | |
Coolant volume | L | 250 | ||
Dimension | mm | 2400*1770*2010 | ||
Total weight | kg | 3800 |
The information on this page is for reference only. Specifications and details may change due to product upgrades or improvements. For more information, please contact us.
Mitsubishi
FANUC
Siemens
SYNTEC
Apr 11 2025
Apr 01 2025