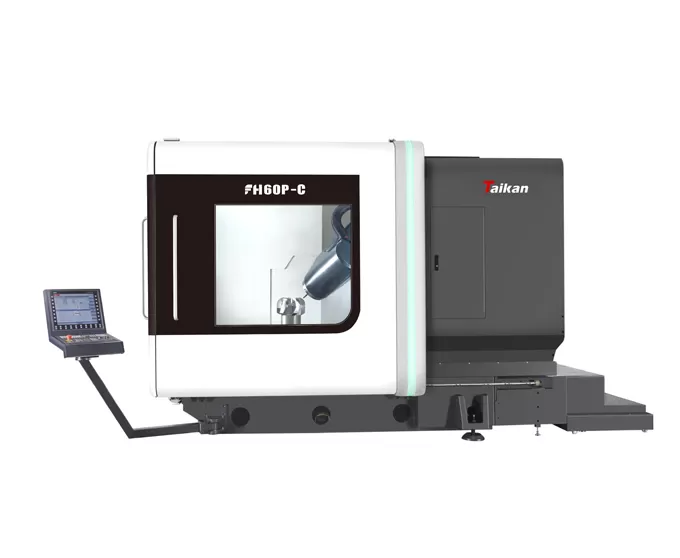
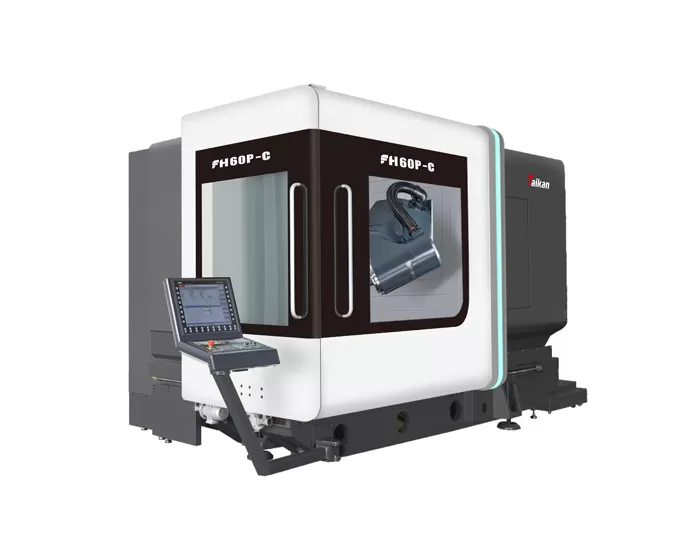
Five-Axis Milling and Turning Machining Center
Optimal Mechanical Casting Design
The bed is made of a new mineral casting structure, while moving parts use Meehanite-grade high-quality cast iron.
Tempered and naturally aged to eliminate internal stresses.
Materials with natural frequency to eliminate vibration-induced processing stresses.
The large-area, high-rigidity column design effectively improves rigidity and static/dynamic precision.
Three-axis hollow cooling ballscrew drive.
Powerful 5-Axis Milling Head
SIGNIFICANTLY IMPROVED AND IMPROVED INTERFERENCE PROFILE AND RIGIDITY
The B-axis with direct drive of DD motor improves rigidity through larger YRT bearing, which can realize high-torque cutting under the linkage state.
Turning and Milling Table
Independently designed and manufactured.
Internal DD motor with zero backlash, direct drive design.
High acceleration and deceleration response characteristics.
Larger YRT bearings for improved rigidity.
High rated drive torque with positioning and clamping device for the worktable.
Supports both milling and turning operations, reducing workpiece handling and improving product precision.
Automatic Tool Change System
Tool selection and change are controlled by a servo motor for more stable and accurate operation.
With Siemens ONE's tool management feature, tool management is more efficient.
The advanced and highly stable 5-axis machine mechanism, with a simple man-machine operation mode, focuses on improving accuracy, performance and efficiency by 30% each, achieving the highest machining performance and part accuracy under high dynamic conditions. From the hardto-cut materials in the aviation industry to the highest surface quality requirements in the mold manufacturing industry, the Feihong five-axis simultaneous milling-turning compound machining center provides the best conditions. Feihong five-axis linkage turning and milling compound machining center can realize multi-form use: vertical and horizontal conversion, milling and turning, one-time clamping, multi-process and multi-angle processing and forming.
Aerospace Impeller Processing
45° Inclined Surface Processing
Turning and Milling Compound One Clamping
Helical Rotor Processing
Vertical Turning Function
Item | FH60P-C |
X/Y/Z axis travel | 600×800×600mm |
Distance from horizontal milling head center to working table | 30~630mm |
Rotary table speed | 350rpm |
Working table size | φ660mm |
Max table load | Milling 2000kg Turning 1000kg |
Swing milling head (B axis) | Standard |
Swing range (0=Vertical/180=Level) | -15°~ +180° |
B axis rated speed | 50rpm |
Distance from vertical spindle nose to table | 150~750mm |
Electric spindle Max. speed | 12000rpm |
Power(S1-100%/40%DC) | 34/42kW |
Torque(S1-100%/40%DC) | 132/192Nm |
Spindle taper | 1:10 Taper |
Tool interface | HSK-A63 |
Tool magazine capacity | 40T |
Max. tool diameter/length/weight | φ85mm/300mm/8kg |
Tool changing time (Tool to Tool) | 4s |
Drilling (Normalizing medium carbon steel) | φ40mm |
Tapping (Normalizing medium carbon steel) | M24 |
Rapid traverse | 40m/min |
X/Y/Z positioning accuracy | 0.006mm |
X/Y/Z repeat positioning accuracy | 0.004mm |
B/C positioning accuracy | 8" |
B/C repeat positioning accuracy | 4" |
Infrared probe | Renishaw OMP60 |
Tool setting gauge | Renishaw NC4F230 |
Machine height (Standard machine) | 2985mm |
Main body occupied area(L*W) | 4300×2600mm |
Tool magazine occupied area (L*W) | 2100×1250mm |
Chip conveyor occupied area (L*W) | 3070×1065mm |
Water tank occupied area(L*W) | 1785×1355mm |
Complete machine occupied area | 5200×3550mm |
Machine weight | 23000kg |
Control system | Siemens ONE |
The information on this page is for reference only. Specifications and details may change due to product upgrades or improvements. For more information, please contact us.
SINUMERIK ONE
Apr 11 2025
Apr 01 2025