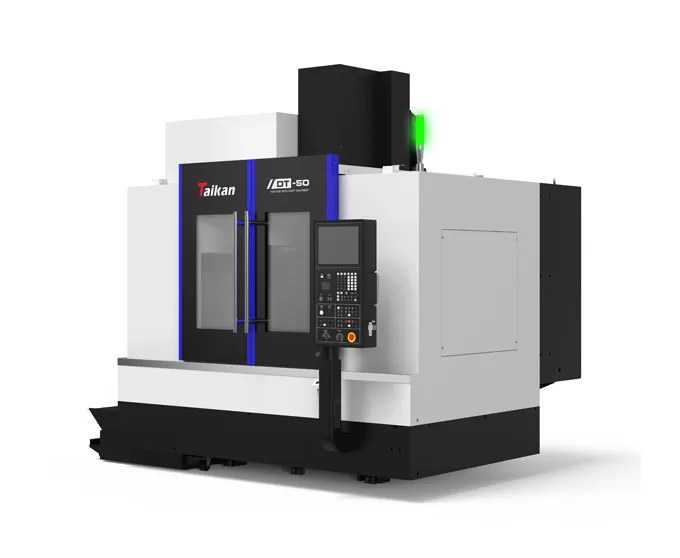
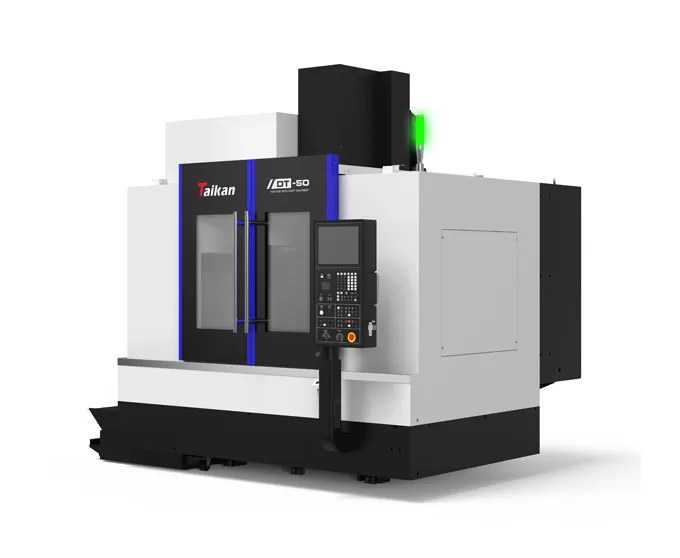
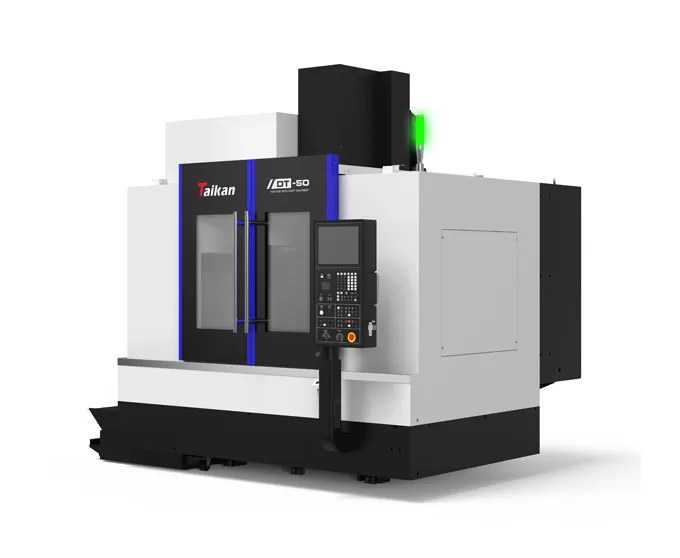
High Rigidity & High Efficiency
High speed, high efficiency and high precision
Full Travel Support Structure
The machine features a T-shaped bed, with the saddle moving left and right on the X-axis and the table moving forward and backward on the Y-axis. The full travel support of the table and saddle eliminates the lateral overhang of traditional C-type vertical machining centers, ensuring better dynamic performance and cutting stability.
Hollow Cooling Ball Screw
The large-diameter precision ball screw features a hollow cooling system and pre-tension design to reduce thermal deformation, improve machining precision, and extend the screw's service life.
Precision High-Speed Spindle Unit
The spindle uses a BBT40-12000r/min direct-drive system with a cooling system to reduce thermal deformation, improve accuracy, and extend bearing life. The spindle front end has a labyrinth seal and air curtain to prevent coolant from entering the bearings, ensuring long-term stability.
Fully Enclosed Tool Magazine
The fully enclosed tool magazine protects the tools from contamination, keeping them clean. The servo-driven ATC system improves tool change speed, accuracy, and stability, boosting machining efficiency.
The machine tool is suitable for the multi-variety, small-batch processing of complex parts such as medium and small-sized box-shaped components, plates, disks, valves, housings, and molds. It is widely used in industries such as precision parts, 5G products, hardware, automotive parts, and medical devices.
Workpiece Example 1
Workpiece Example 2
Workpiece Example 3
Workpiece Example 4
Workpiece Example 5
Workpiece Example 6
Name | Unit | DT50 | Remarks | ||
Travel | Table travel(X-axis) | mm | 850 | ||
Saddle travel(Y-axis) | mm | 500 | |||
Spindle box travel(Z-axis) | mm | 500 | |||
Distance from spindle nose to table surface | mm | 150-650 | |||
Distance spindle center to column guide surface | mm | / | |||
Table | Table size | mm | 1100*450 | ||
Table loading | kg | 600 | |||
T-SLOT(QTY-Width*Space) | mm | 3-18*125 | |||
Spindle | Motor power (S1/S6) | kW | 11/18.5 | ||
Motor torque (S1/S6) (rated/short-time) | N.m | 52.5/118 | |||
Rotary speed | r/min | 50~12000(direct) | |||
Spindle diameter | mm | Ф150 | |||
Spindle tapper | / | BBT40 | |||
Drive | Motor power X/Y/Z | kW | 3.0/3.0/3.0 | ||
Speed | X/Y/Z axis rapid speed | m/min | 48/48/48 | ||
Accuracy | Position accuracy(X/Y/Z) | mm | 0.006/0.006/0.006 | VDI 3441 | |
Repeatability(X/Y/Z) | mm | 0.004/0.004/0.004 | |||
Tool magazine | Tool capacity | T | 30 | ||
Max. weight | kg | 8 | |||
Max. length | mm | 350 | |||
Max. allowable torque | Nm | ≤10.19 | |||
Max. diameter(full/adjacent) | mm | Ф80/Ф150 | |||
Others | CNC system | / | FANUC 0i MF PLUS | ||
Gas source | Flow | L/min | ≥280(ANR) | ||
Air pressure | MPa | 0.6-0.8 | |||
Equipment capacity | KVA | 25 | |||
Machinery size | mm | 3028*2914*2935 | Corresponding X*Y*Z axis | ||
Machine weight(approx.) | kg | 5600 |
The information on this page is for reference only. Specifications and details may change due to product upgrades or improvements. For more information, please contact us.
Mitsubishi
FANUC
Siemens
Taikan
Apr 11 2025
Apr 01 2025